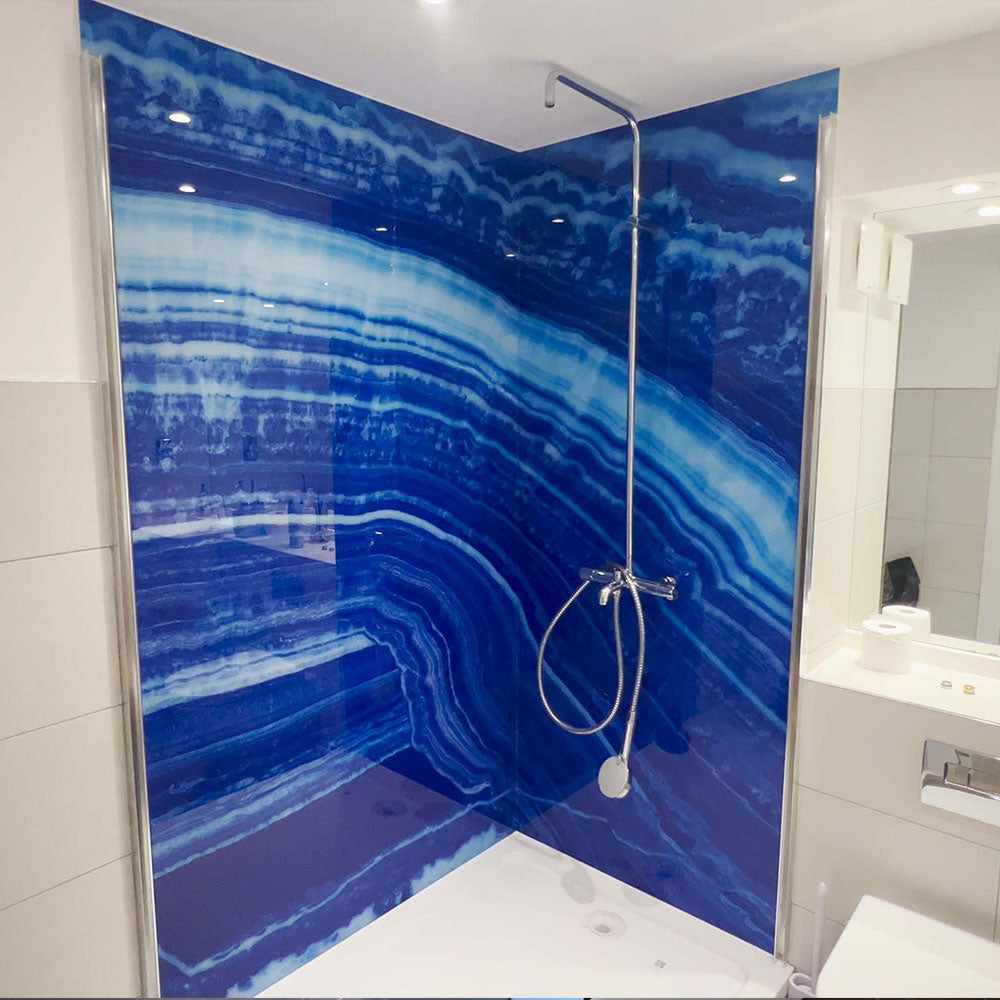
Manufacturing glass shower splashbacks in the UK involves a few urgent advances, every one of which requires accuracy and skill to ensure that the completed item is both useful and satisfying to the eye. The connection consolidates best-in-class development with gifted craftsmanship, ensuring fine-quality results. Here is an outline of the cycle:
Measurement and design: The assembling system starts with the planning stage. Specifications, such as dimensions, colors, and any special requirements, are provided by clients or designers. Exact estimations are basic to guarantee an ideal fit in the shower region. Computer-aided design (CAD) software is frequently used to create digital templates, ensuring precision.
Glass Determination: Top caliber, hardened (treated glass) is chosen for its strength and well-being properties. Hardened glass is favored because it is more grounded than standard glass and, whenever broken, breaks into little, less hazardous pieces. The glass picked is regularly low-iron, clear, or shaded, contingent upon the client's inclination.
Cutting: The chosen glass sheets are sliced to estimate utilizing progressed CNC machines. These machines ensure precise cutting according to the digital templates created earlier. CNC machines can deal with many-sided shapes and openings for apparatuses, giving the specific particulars expected to be established.
Edge Cleaning and Molding: After cutting, the edges of the glass are cleaned to eliminate sharpness and make a smooth completion. This step is essential for both security and tasteful purposes. Particular machines clean the edges, which can likewise slope or be adjusted by the plan determinations.
Toughening: After the Glass Shower Splashbacks in the UK have been cut and cleaned, they go through a hardening interaction. This incorporates warming the glass to over 600°C and cooling it a while later. This cycle builds the strength of the glass altogether, making it appropriate for use in conditions like washrooms where security is central.
Painting and Coating: To make hued splashbacks, the rear of the hardened glass is painted utilizing expert glass paints. This should be possible physically or by using mechanized shower frameworks to guarantee even inclusion. The paint is then heated guarantee strength to and protection from dampness and cleaning synthetics. Some splashbacks may also include printed designs or patterns, applied using digital printing technology.
Quality Examination: Each Glass Shower Splashback in the UK piece goes through a thorough quality review cycle to check for any deformities like breaks, scratches, or paint defects. Only glass that meets strict quality standards is approved for the next stage.
Packaging and Delivery: The finished glass splashbacks are carefully packaged to prevent damage during transit. Custom packaging solutions, such as foam inserts and sturdy boxes, are used to protect the glass. The splashbacks are then delivered to the customer or installer.
Installation: While the establishment isn't normally essential for the assembling system, producers frequently give point-by-point directions or expert establishment administrations. Appropriate establishment guarantees that the splashbacks are safely and accurately fitted, giving enduring execution and style.
The manufacture of Glass Shower Splashbacks in the UK is a careful cycle that consolidates cutting-edge innovation with master craftsmanship. From planning and slicing to hardening and getting done, each step is essential to creating an excellent item that fulfills both well-being guidelines and stylish requests. The end product is a long-lasting and stylish addition to contemporary bathrooms that demonstrates the precision and care that went into its creation.
Write a comment ...